Material Selection
First of all, since this is a remodel, a lot of my materials are already here in the house. The idea is not to tear out things that don't need tearing out. That, of course, must be balanced out with the fact that some things are old, ugly, or just don't go with the design. I'll go through some of the main materials and items that will be brought in.
Paint - Paint is one of the major sources of poor indoor air quality. Long after the smell goes away, it can still be off-gassing toxic substances into your home. The majority of our paint will be Yolo Colorhouse. This product went beyond simply eliminating VOC's and earned Green Seal GS 11 2008 certification. Green Seal is a very trusted and stringent certification program. I also plan to do some accent walls with American Clay, a plaster made of all natural aggregates, clays, and pigments. Much of the product comprised post-industrial aggregate waste from rock quarries and sea shells.
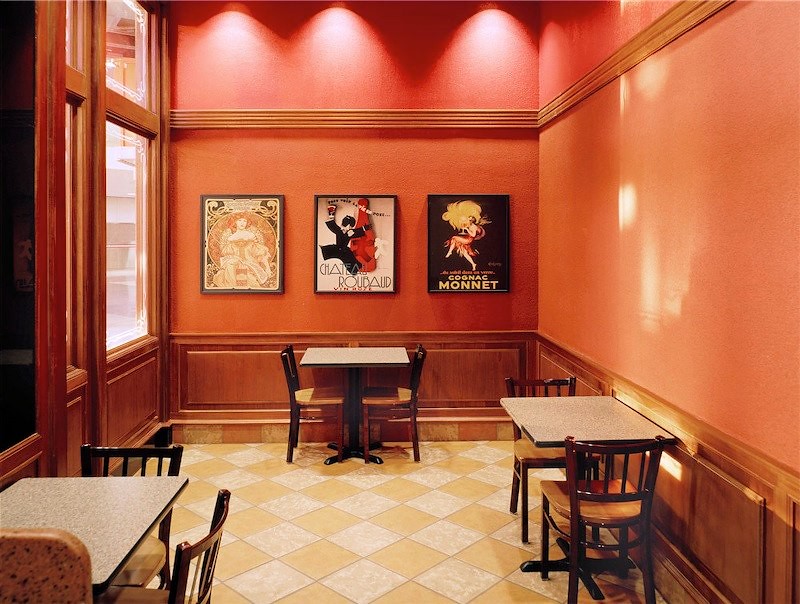
American Clay Wall Plaster
Cabinets - After some consideration, we've decided that our current kitchen cabinets aren't going to work in our design. These ones will be taken out and reused in my tool room. We haven't decided on the replacements yet, but the main thing will be to ensure that the wood was sourced responsibly. The Forest Stewardship Council has made it very easy to do this. We're also going to check out Dean Innovations, which is where I have been getting our garden soil, compost, and gravel. They make flooring, cabinets, and dimensional lumber from local fir trees that have fallen over due to natural causes; windstorms, landslides, old age, etc.
Counters - As I mentioned a few posts back, we are using Paper Stone for our kitchen counters and the bar. This material is made of 100% post-consumer, FSC certified, recycled paper. The paper is held together with a non-toxic resin and homogenized using heat and pressure. The resulting product is an impervious surface that is certified food safe by the NSF. The counters are closer to the durability of real stone than wood, but can be sanded, cut, and edged using normal wood working tools.
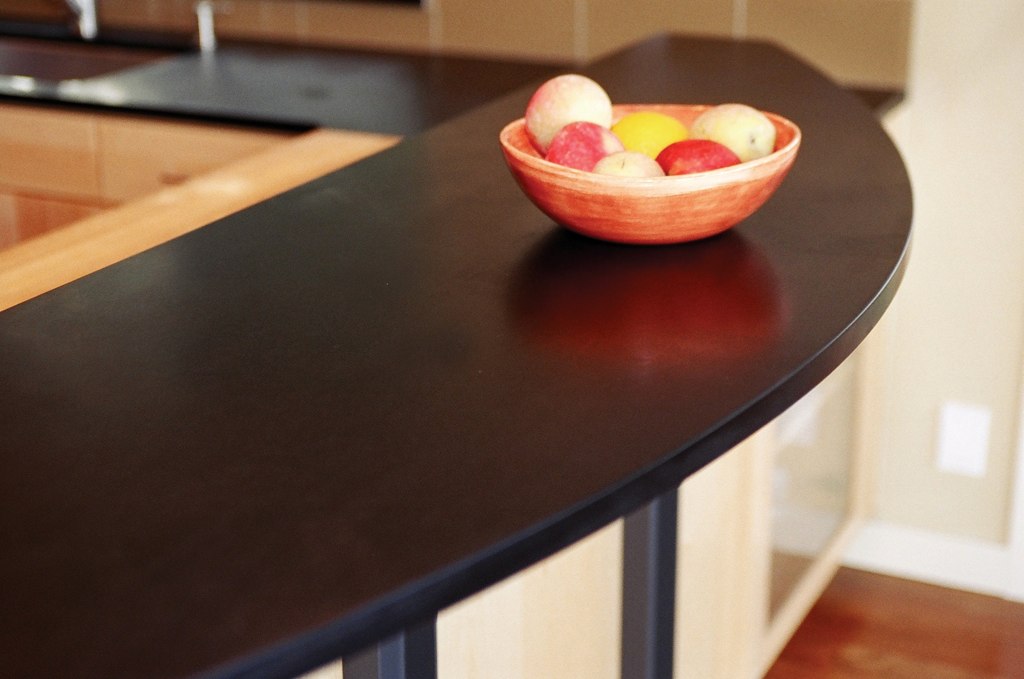
Paper Stone Countertops
Floors - The original living room floor will be refinished. Unfortunately, the kitchen floors are starting to look like a lost cause and the rest of the house is just plywood subfloor at the moment. The kitchen will most likely get tile, but we haven't started to research our options on that yet. The bedrooms will be getting wood floors. These aren't picked out yet, but we will be sure that they are FSC certified and/or salvaged and that the adhesives and finishes don't contain any harmful substances. Although there are some better carpeting options on the market these days, we still don't plan on having any in the house. If you've ever ripped carpet out, you probably feel the same way.
Interior Walls - Most of our interior walls will stay in tact with nothing more than a fresh coat of paint (someone really beat this house with an ugly stick before we moved in). The bathrooms are getting gutted and the new walls will be a Magnesium Oxide panel, or MgO Board. One available here locally is GreenE-Board, but I haven't done a lot of research on them in particular. The advantage of this product over conventional drywall is that it has a much lower embodied energy, better fire rating, and is mold and moisture resistant. It makes much more sense, especially for bathrooms, and can even be used on the floors as tile backer.
Roof - I will be replacing the existing asphalt roof with a standing seam metal roof. While metal has a high embodied energy, the benefits are numerous. It doesn't leech chemicals into the rainwater, it lasts a lifetime, it will never leak if installed correctly, and it can be recycled if and when it's ever removed. We were planning on doing this soon, but there is quite a project that goes along with it fixing the roof framing, upgrading insulation, and replacing the ceiling. This will have to wait until next year.
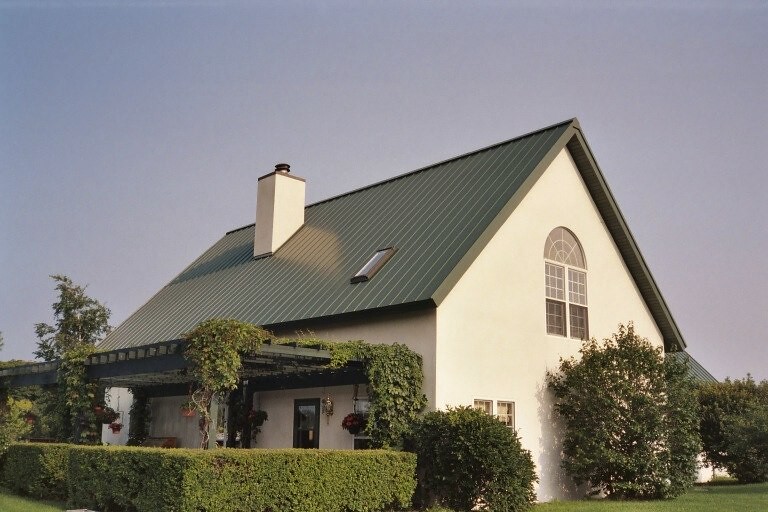
Standing seam metal roof, Not my favorite color
Siding - We haven't picked out our exact siding yet, but we are researching options and weighing out the benefits. Fiber-cement products, such as Hardie, are very affordable and make many sustainability claims. I do agree with some of their points. These products are durable, hold paint longer than wood, and don't rot or get eaten by pests. One of their downsides is being very resource-intensive in production. Another reason that we haven't decided yet is that I wanted to use a salvaged cedar siding with a natural weathered look and Annie prefers painted siding. This one remains to be settled...
Windows - We haven't picked an exact window manufacturer yet, but we will definitely be going with a non-vinyl option. Why not vinyl? Read about the horrors of PVC here. The main options left would be fiberglass, wood, and aluminum (or a combination of those). There are some great modern aluminum frame options available now with advanced frame design to eliminate thermal bridging through the frame. Windows are also available with a variety of options concerning U-Factor (insulation) and Low-E (solar ray deflection). This is something I'll go into greater detail about in a later post.
Stove - We can't buy all vintage appliances, but I'm sure glad we found this beautiful mid-century O'Keefe and Merrit. That's one less item that had to be manufactured overseas and shipped here. Plus just can't get this look anymore unless you plan on dropping $4,000+ on a reproduction.

Annie finally got the stove she always wanted
Recycling
I've been making an effort to reuse everything possible so far. This isn't something that can always be planned for ahead of time, so I'm keeping organized piles of materials as I pull them out and taking from them when I can. For example, I was able to replace the rotten/beetle eaten subfloor using 2x4's I pulled out of a wall I tore down. Things I know we won't use are being taken to proper recycling or reuse facilities as they stack up. The tubs, sinks, mirrors, etc from the bathrooms will all go to The ReBuilding Center.

This stuff all got sorted and a lot of the lumber is being reused on site. Most of the remaining unusable debris will get reused off-site or recycled. Very little, if any, will end up at the dump.
As you can see, a lot of though and research must go into these plans. Various trusted certification labels are starting to be seen on products more and more, which help tremendously in determining if it's right for a green building project. A great resource for me has been EcoHaus, Portland's premier green building supply store. They are very careful about what goes on their shelves and the staff is extremely friendly, knowledgable, and non-pretentious.
So far, we feel very successful in working toward our goal of choosing products that have a low impact on the environment on their way to us, do not negatively affect air quality or health, are made to last a long time, and can be reused or recycled at the end of their useful life here.
Stay tuned for PART 2, where I will discuss the plan for resource efficiency and conservation.
No comments:
Post a Comment